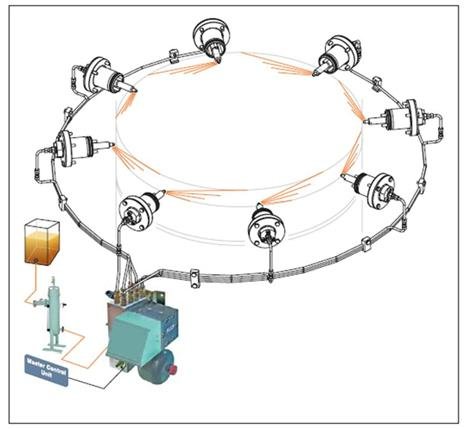
Contents
- Introduction to Cylinder Lubrication
- Purpose and Function of Cylinder Lubrication
- Cylinder Lubrication in Low-Speed Diesel Engines
- Cylinder Lubrication in Four-Stroke Trunk Piston Engines
- Type of Oil Used in Cylinder Lubricating Systems
- Total Base Number (TBN) in Lubricating Oils
- Correct Feed Rate for Cylinder Lubrication
- Impact of Under-Lubrication and Over-Lubrication
- Preventing Acid Condensation in the Combustion Chamber
- Engine Run-In Procedures
- Components of a Lube Oil System
- References
1. Introduction to Cylinder Lubrication
Cylinder lubrication is crucial for the efficient operation of marine diesel engines, particularly those running on residual fuels containing sulphur. Effective lubrication helps prevent mechanical wear, neutralize acids, and clean combustion residues, ensuring optimal engine performance and longevity.
2. Purpose and Function of Cylinder Lubrication
Cylinder lubrication serves multiple purposes in marine diesel engines:
- Oil Film Creation: Prevents metal-to-metal contact between the cylinder liner and piston rings.
- Acid Neutralization: Neutralizes sulfuric acid to control corrosion.
- Cleaning: Keeps the cylinder liner and piston ring pack clean, preventing malfunction and damage from combustion and neutralization residues.
3. Cylinder Lubrication in Low-Speed Diesel Engines
For low-speed main propulsion diesel engines, cylinder lubricating oil is injected during the compression stroke. This timing ensures the oil lubricates effectively without evaporating due to high temperatures or causing a scraping effect during the expansion stroke. Proper lubrication requires:
- Correct Timing: Lubricating oil is admitted when the piston, piston rings, and liner are relatively cool and moving upward.
- Prevention of Evaporation: Injecting oil during the compression stroke prevents it from evaporating too quickly.
4. Cylinder Lubrication in Four-Stroke Trunk Piston Engines
In four-stroke trunk piston engines, cylinder lubrication methods vary by engine size and design:
- Splash Lubrication: Oil is splashed from the revolving crankshaft.
- Inner Lubrication: Oil is supplied from the piston side.
- Outer Lubrication: Oil is delivered by an external device from the cylinder liner side.
In these engines, the cylinder lubricating oil is the same as the system oil used for bearing lubrication and cooling. The oil is partially consumed in the combustion space but primarily recycled through an oil scraper ring, which returns excess oil to the oil pan for cleaning and reuse.
5. Type of Oil Used in Cylinder Lubricating Systems
The oil used in cylinder lubrication must:
- High Viscosity: Form a robust lubricating film between the liner and piston rings.
- Heat Resistance: Withstand combustion temperature variations and handle combustion products.
- Alkalinity: Typically an SAE 50 viscosity oil with a TBN (Total Base Number) suitable for the sulphur content of the fuel used. TBN values vary based on fuel sulphur content, with higher TBN oils (up to 70 or more) used for fuels with higher sulphur content.
6. Total Base Number (TBN) in Lubricating Oils
TBN (Total Base Number) measures the alkalinity of the lubricating oil, indicating its ability to neutralize acids formed during combustion, especially when using high-sulphur fuels. TBN is crucial because it helps prevent corrosion and maintain engine cleanliness.
- Measurement: TBN is measured in milligrams of potassium hydroxide per gram of oil (mg KOH/g).
- Examples:
- Low Sulphur Fuel (0.5 to 1%): TBN 20-25
- High Sulphur Fuel (over 1.5%): TBN 70 or higher
7. Correct Feed Rate for Cylinder Lubrication
Establishing the correct feed rate is crucial for effective cylinder lubrication:
- Manufacturer Recommendations: Follow engine builder’s guidelines for feed rates.
- Optimal Lubrication: Proper feed rates ensure the formation of an adequate lubricating film, preventing both over-lubrication and under-lubrication.
8. Impact of Under-Lubrication and Over-Lubrication
Under-Lubrication:
- Risks: Corrosion, contamination build up, metal-to-metal contact (scuffing).
Over-Lubrication:
- Risks: Excessive oil loss, hydraulic lock of piston rings, chemical bore polish, mechanical bore polish.
9. Preventing Acid Condensation in the Combustion Chamber
Proper operation of the cooling system is essential to prevent sulfuric acid condensation, which depends on factors such as combustion pressure, liner temperature, sulphur oxide concentration, and intake air humidity. Maintaining recommended scavenge air temperatures is vital to avoiding condensation and ensuring efficient combustion.
10. Engine Run-In Procedures
Effective cylinder lubrication depends on the initial run-in procedure of the engine:
- Proper Run-In: Ensures good wear of the cylinder liner and piston rings, creating an optimal gas seal and lubrication.
- Lubricant and Feed Rate: Use specific lubricants and feed rates as recommended by the engine manufacturer during the run-in period.
11. Components of a Lube Oil System
A typical marine engine lube oil system includes:
- Lube Oil Pump: Circulates oil throughout the engine.
- Oil Cooler: Removes excess heat from the oil.
- Filters: Remove contaminants from the oil.
- Pressure Regulator: Maintains appropriate oil pressure.
- Lube Oil Tank: Stores the lubricating oil.
- Distribution Manifold: Directs oil to various engine components.
12. References
- Marine Diesels Info
- Cowley, “The Running and Maintenance of Marine Machinery”
- Sanyal, “Principles and Practice of Marine Diesel Engines”
- Christensen, “Lamb’s Question and Answers on Marine Diesel Engines”
- Reeds Marine Engineering Series, Vol. 12, “Motor Engineering Knowledge for Marine Engineers”
- Wärtsilä
For more detailed articles and information on maritime tools and technologies, visit MaritimeHub.com