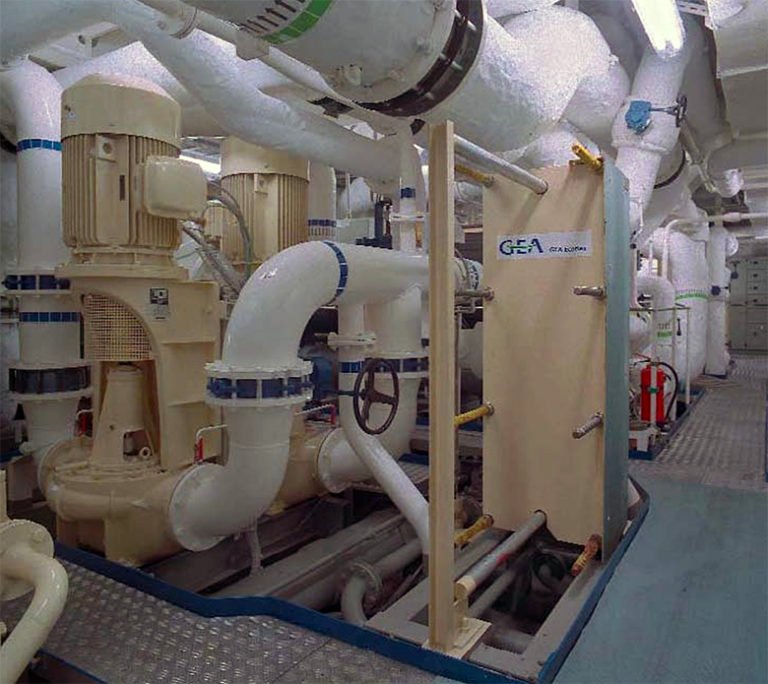
Contents
- Introduction to Heat Exchangers
- Uses of Heat Exchangers on Ships and Oil Rigs
- Types of Heat Exchangers
- 3.1 Shell and Tube Heat Exchangers
- 3.2 Plate Heat Exchangers
- 3.3 Air Cooled Heat Exchangers
- 3.4 Double Pipe Heat Exchangers
- 3.5 Spiral Heat Exchangers
- Pros and Cons of Different Types of Heat Exchangers
- 4.1 Shell and Tube Heat Exchangers
- 4.2 Plate Heat Exchangers
- 4.3 Air Cooled Heat Exchangers
- 4.4 Double Pipe Heat Exchangers
- 4.5 Spiral Heat Exchangers
- Systems Using Heat Exchangers on Ships
- Materials Used in the Construction of Heat Exchangers
- Popular Manufacturers and Models
- Maintenance Recommendations for Heat Exchangers
- Common Issues and Solutions
- Sizing of Heat Exchangers
- Conclusion
- References
1. Introduction to Heat Exchangers
Heat exchangers are critical components used in various systems on ships and oil rigs to transfer heat between two or more fluids. This process enhances efficiency, conserves energy, and ensures the optimal functioning of numerous mechanical and electrical systems.
2. Uses of Heat Exchangers on Ships and Oil Rigs
On ships and oil rigs, heat exchangers serve several essential purposes, including:
- Cooling: Engines, generators, and other machinery require efficient cooling systems to maintain operational temperatures.
- Heating: Preheating fuel or other fluids to ensure proper viscosity and flow.
- Waste Heat Recovery: Capturing waste heat from exhaust gases or other processes to improve overall energy efficiency.
- HVAC Systems: Regulating temperatures within living and working spaces for comfort and safety.
- Oil Cooling: Cooling lubricating oil in engines and other equipment to maintain proper lubrication and performance.
3. Types of Heat Exchangers
3.1 Shell and Tube Heat Exchangers
Description: Comprise a series of tubes, one set carrying the hot fluid and the other the cold fluid, housed within a cylindrical shell.
3.2 Plate Heat Exchangers
Description: Made up of multiple thin, corrugated plates stacked together, with hot and cold fluids flowing through alternate channels.
3.3 Air Cooled Heat Exchangers
Description: Utilize air to cool the fluid inside the heat exchanger tubes, often employing fans to increase airflow.
3.4 Double Pipe Heat Exchangers
Description: Consist of one pipe inside another, where one fluid flows through the inner pipe and the other fluid flows through the annular space between the pipes.
3.5 Spiral Heat Exchangers
Description: Features two spiral channels, one for each fluid, which enhance heat transfer through increased surface area and turbulence.
4. Pros and Cons of Different Types of Heat Exchangers
4.1 Shell and Tube Heat Exchangers
Pros:
- High-pressure handling capacity.
- Suitable for large heat transfer areas.
- Versatile and can handle a wide range of fluids.
Cons:
- Large footprint.
- Higher maintenance complexity.
- Potential for fouling.
4.2 Plate Heat Exchangers
Pros:
- High heat transfer efficiency.
- Compact design.
- Easy to clean and maintain.
Cons:
- Limited pressure and temperature range.
- Potential for gasket leakage.
- Not suitable for fluids with large particles.
4.3 Air Cooled Heat Exchangers
Pros:
- No need for a cooling water supply.
- Suitable for remote locations.
- Lower operational costs.
Cons:
- Larger physical size.
- Less efficient in high ambient temperatures.
- Noisy operation due to fans.
4.4 Double Pipe Heat Exchangers
Pros:
- Simple construction.
- Easy to clean and maintain.
- Suitable for small to moderate heat transfer areas.
Cons:
- Limited to lower heat transfer rates.
- Bulkier for larger applications.
- Potential for thermal expansion issues.
4.5 Spiral Heat Exchangers
Pros:
- High heat transfer efficiency.
- Compact and space-saving design.
- Resistant to fouling.
Cons:
- Complex manufacturing process.
- Higher initial cost.
- Limited to specific applications.
5. Systems Using Heat Exchangers on Ships
Heat exchangers are used in various systems on ships, including:
- Main Engine Cooling: To maintain the engine temperature within optimal operating ranges.
- Freshwater Generators: To produce freshwater from seawater using waste heat.
- Fuel Oil Preheating: To ensure proper viscosity of fuel before combustion.
- HVAC Systems: For climate control within the ship.
- Lubricating Oil Cooling: To maintain the proper temperature of lubricating oil.
6. Materials Used in the Construction of Heat Exchangers
Heat exchangers are constructed from a variety of materials to suit different applications and environmental conditions:
- Stainless Steel: Highly resistant to corrosion and suitable for high-temperature applications.
- Titanium: Offers excellent corrosion resistance, especially in seawater applications, but is more expensive.
- Copper: Known for its high thermal conductivity and corrosion resistance.
- Aluminum: Lightweight with good thermal conductivity, often used in air-cooled heat exchangers.
- Nickel Alloys: Used for high-temperature and high-corrosion environments, such as chemical processing and offshore applications.
7. Popular Manufacturers and Models
Alfa Laval
- Model: M10-BW Plate Heat Exchanger
- Features: High efficiency, compact design, and easy maintenance.
- Cost: Approximately $5,000 to $20,000 depending on size and configuration.
GEA Group
- Model: NT Series Plate Heat Exchangers
- Features: Advanced plate design for high heat transfer efficiency.
- Cost: Approximately $10,000 to $30,000.
Kelvion
- Model: K°Bloc Shell and Tube Heat Exchanger
- Features: Robust design for high-pressure applications.
- Cost: Approximately $20,000 to $50,000.
SPX FLOW
- Model: APV ParaFlow Plate Heat Exchanger
- Features: High efficiency with a wide range of applications.
- Cost: Approximately $15,000 to $35,000.
Tranter
- Model: Superchanger Plate & Frame Heat Exchanger
- Features: Easy to clean and maintain with high thermal efficiency.
- Cost: Approximately $8,000 to $25,000.
8. Maintenance Recommendations for Heat Exchangers
Shell and Tube Heat Exchangers:
- Maintenance Interval: Every 12-24 months
- Tasks: Inspection, cleaning of tubes, checking for leaks, pressure testing.
Plate Heat Exchangers:
- Maintenance Interval: Every 6-12 months
- Tasks: Plate inspection, cleaning, gasket replacement, pressure testing.
Air Cooled Heat Exchangers:
- Maintenance Interval: Every 12 months
- Tasks: Fan inspection, cleaning fins, checking for leaks, ensuring proper airflow.
Double Pipe Heat Exchangers:
- Maintenance Interval: Every 12-24 months
- Tasks: Inspection, cleaning of inner and outer pipes, checking for leaks, pressure testing.
Spiral Heat Exchangers:
- Maintenance Interval: Every 12-24 months
- Tasks: Cleaning spiral channels, checking for fouling, inspecting for leaks.
9. Common Issues and Solutions
Fouling:
- Issue: Accumulation of deposits on heat transfer surfaces.
- Solution: Regular cleaning and using anti-fouling coatings.
Leaks:
- Issue: Fluid leakage due to gasket failure or corrosion.
- Solution: Regular inspection, timely gasket replacement, and use of corrosion-resistant materials.
Pressure Drop:
- Issue: Excessive pressure drop across the heat exchanger.
- Solution: Ensuring proper design, regular cleaning, and maintenance.
Thermal Expansion:
- Issue: Damage due to differential thermal expansion.
- Solution: Incorporating expansion joints and regular inspection.
10. Sizing of Heat Exchangers
The size of a heat exchanger is determined based on several key factors, including the required heat transfer rate, temperature differences, fluid properties, and flow rates. The basic formula used for sizing is:
Q=U×A×ΔTlmQ = U \times A \times \Delta T_{lm}Q=U×A×ΔTlm
Where:
- QQQ = Heat transfer rate (W)
- UUU = Overall heat transfer coefficient (W/m²·K)
- AAA = Heat transfer area (m²)
- ΔTlm\Delta T_{lm}ΔTlm = Log mean temperature difference (K)
Example Calculation:
- Determine the heat transfer rate (QQQ) needed for your application.
- Calculate the log mean temperature difference (ΔTlm\Delta T_{lm}ΔTlm) based on the inlet and outlet temperatures of both fluids.
- Estimate the overall heat transfer coefficient (UUU) based on the type of heat exchanger and fluids involved.
- Solve for the heat transfer area (AAA) using the formula.
This formula provides a starting point. Detailed design often requires iterative calculations and considerations of factors such as flow arrangement, fouling factors, and material properties.
MaritimeHub.com